Can Warehouse Automation Make the Picker's Job Better?Can Warehouse Automation Make the Picker's Job Better?
With demand for shipped products increased during the COVID-19 pandemic, the move toward warehouse automation could accelerate, but is that good or bad news for warehouse workers?
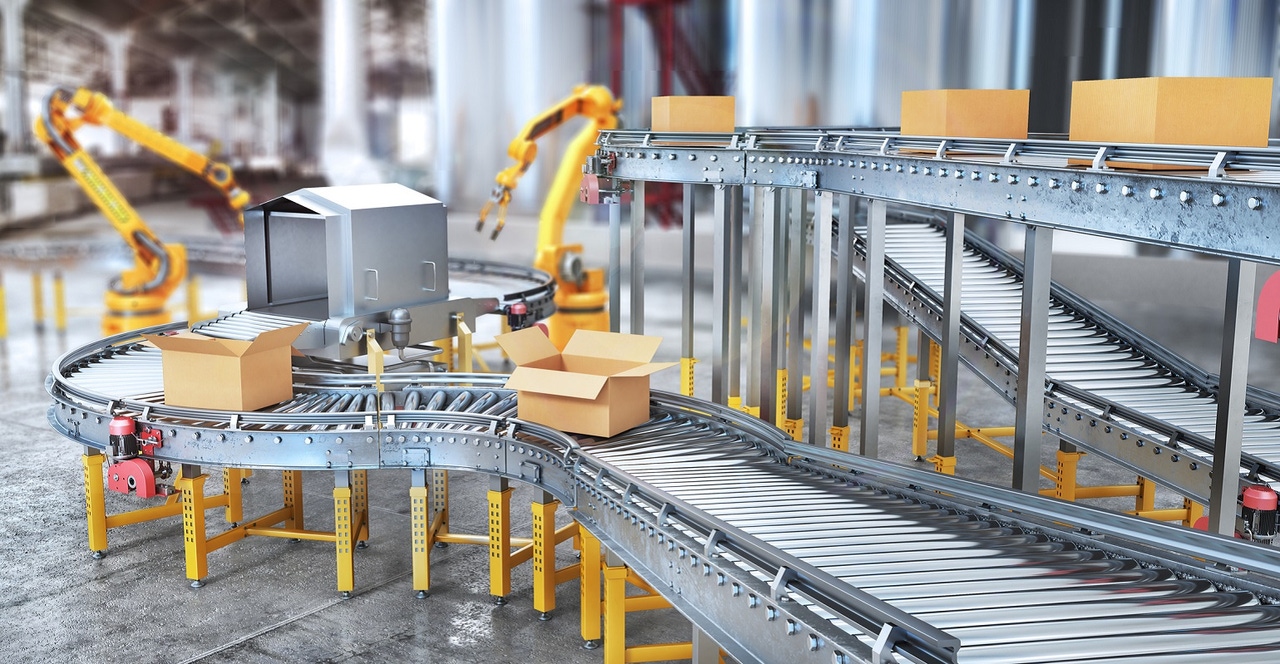
Working conditions in warehouses were a news story before COVID-19. Amid growing efforts to unionize and gain greater wages and workplace protections, workers at warehouses for companies such as Amazon have gone on strike, protested high injury rates and called out grueling conditions.
Now, amid a global pandemic, it seems that warehouse automation, the thing some feared would eliminate these jobs altogether, may have a role to play in making them better.
Data, software, automation and analytics already play a significant role in many warehouse jobs. At Amazon, for example, software monitors employees, pinging them when they’ve done something incorrectly and tracking how long it takes them to complete tasks. At the same time, robots do easily automated tasks like moving bins of products from one location to another.
But the workers themselves are also already doing what they can to automate. A New York Times article detailed how workers decide where to store items in order to reduce their movements and therefore speed up their packing time, for example. At the same time as the employees are making these decisions, software is reminding them when they do something they are or are not allowed to do — if they store a heavy object too high up or place an item in a bin next to another with the same thing in it.
A recent report from MIT and IBM Watson AI Lab found that the risk of replacement of human workers comes less from robots than it does from algorithms. Further, while some workers will lose their existing jobs, not all will — instead, some jobs will change through artificial intelligence (AI) and machine learning (ML) as some tasks become increasingly automated.
Can Automation Improve Working Conditions?
But as things currently work, the system and its extreme focus on optimization already seem to make employees feel like little more than robots. The hope of some of the people working on warehouse automation is that algorithm-driven robotics will do the tasks that require that automation, freeing humans up to focus on the work that humans are best suited for.
“The growth of automation in warehouses is widely touted as it helps to drastically improve processes, productivity and efficiency, especially during periods of increased demand,” said Adam Kline, senior director of product management at Manhattan Associates. “When augmented by automation, warehouse workers are freed up to focus on more strategic initiatives throughout the distribution center, thus boosting productivity overall.”
Consider Covariant, a Berkeley, Calif.-based robotics startup. The company has developed an AI-powered robotic arm for warehouse giants such as Knapp and Obeta. Warehouse tasks tend to require either arms or legs — consider the task of packing a box versus moving a cart full of boxes to a shipping dock.
At this point, robotic automation in warehouses has mostly focused on the work that requires legs. Mechatronics, the work that requires arms, is more difficult, and that’s where Covariant says it has made significant progress.
Humans Still Wanted
For Covariant, the challenge of developing the algorithm that powers the robotic picker arms is that it has to work with a wide variety of products, in packaging that might change without notice and could be sitting at any angle on a shelf. Traditional robotic arms can do the same movement over and over — e.g., screw in the same screw in the same spot — but don’t deal well with deviation. That’s where AI — specifically, reinforcement learning — comes in.
Reporting done by MIT Technology Review said that Covariant’s algorithms can now handle 95% of the products in an Obeta warehouse, with humans handling the rest. It’s a reminder that the work already automated in some warehouses requires human intervention.
At Amazon, mistakes sometimes happen with the robot transporters — an item might fall out of a bin along its way, for example. AI and ML still aren't great at dealing with the unexpected. An autonomous car might take too long to realize an object in its path is a person and not a ball; a robot might stop along its path if something it can’t identify gets in its way. Humans might not be needed when everything goes smoothly, but that frees them up to solve problems when it doesn’t.
Of course, there is always that one concern about automation to consider — that it will eliminate jobs. Reuters reporting on Amazon from last year indicates that some jobs will be lost as the software driving automation for warehouses gets smarter and more reliable. And a Brookings Institute report found that higher-paid urban employees may actually be at more risk of automation-related job loss. Whether those jobs move to other areas of the affected companies remains to be seen.
But during the ongoing global pandemic, some of the argument in favor of this automation is being made in real time. Fewer humans required on the floor means better social distancing, for example. And with companies like Amazon dealing with a huge number of orders, automation can reduce the human burden, freeing employees up to work on other problems, Kline said.
“These technologies can improve conditions for workers by taking over some of the hands-on, labor-intensive warehouse activities, ensuring that warehouse workers are as contact-free as possible,” he said.
“Working on a ‘man + machine’ model not only allows organizations to better utilize all resources, including automation and employees, it also allows them to put worker safety at the forefront of its operations, which should be a No. 1 priority,” Kline said.
About the Author
You May Also Like