How the Industrial Internet Consortium Is Making IIoT RealHow the Industrial Internet Consortium Is Making IIoT Real
The executive director of the Industrial Internet Consortium provides an update on the group’s testbeds and the IIoT market adoption at large.
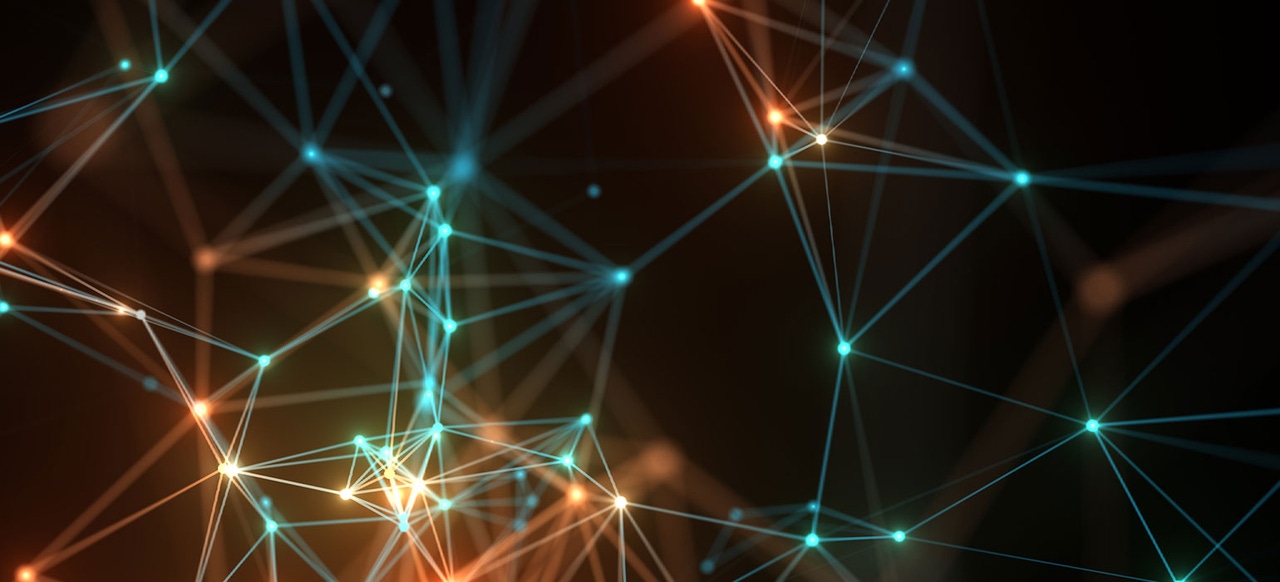
The Industrial Internet Consortium takes an eminently pragmatic approach to IoT. Instead of theorizing about how IoT technology might shape the global economy at some point in the future, the group works with its members to launch projects — testbeds — to learn for themselves.
The approach bears a strong resemblance to the scientific method: Develop a hypothesis and test it with experimentation. Then, repeat the process as needed. The focus of IIC’s testbed programs is on central problems for industries ranging from agriculture to health care to manufacturing. To qualify for IIC’s testbed program, an organization must have a firm business case and ensure their project help provide data relevant to IIC’s theoretical IIoT frameworks. In addition, IIC testbeds must include security by design and, ultimately, provide tangible results.
We recently had the chance to catch up with Richard Soley, Ph.D., executive director of the Industrial Internet Consortium at Hannover Messe, who shared his thoughts on the ongoing collaboration with the German IIoT group Plattform Industrie 4.0, IIC’s growing number of testbeds and overall industrial IoT adoption.
How is the partnership going between Plattform Industrie 4.0 and the Industrial Internet Consortium?
Soley: It is going extremely well. The Industrial Internet Consortium announced we were going to work together about three years ago. Four years ago, the German newspaper Frankfurter Allgemeine Zeitung (FAZ) published an article that basically said the IIC was seeking to compete against German industrial sector. A couple of weeks after that article was published, one of my friends from the German Federal Ministry for Economic Affairs and Energy called me and said: “Staatssekretär Matthias Machnig wants to speak with you as soon as possible.” Later, after I walked into his office and he said: “Dr. Soley, I have a list of questions for you and they were directly from the FAZ article. He gets to the middle of the list, and he asks: ‘Is it true the American government gave you $100 million?’ And I replied: Staatssekretär Machnig, if the American government had given me $100 million, you and I would not be speaking.” He takes the list and crumples it and throws it in the trash. We have been good friends ever since.
The Plattform Industrie 4.0 group doesn’t have an individual existence. It is part of the German Federal Ministry for Economic Affairs and Energy, which, incidentally, has a new Staatssekretär.
So the Industrial Internet Consortium and the Plattform decided to collaborate and create technical working groups to focus on things like security, interoperability and architecture. And I have to say: many people were skeptical in the beginning, but the groups have been meeting for two and a half years every two weeks on the phone and every six months face to face and doing outstanding work. The architecture, security and vocabulary groups are meeting constantly.
The architecture group published a paper on interoperability between Reference Architectural Model Industrie 4.0 (RAMI 4.0) and IIC, and it really works.
The security group is between the two groups has also done excellent work.
The one point of contention has been testbeds. Our focus is on testbeds but their focus hasn’t been. They have no process of approving testbeds.
[Internet of Things World is where IoT is put into action, demonstrating the best case studies for every vertical, from manufacturing to the smart home. Get your tickets and free expo passes now.]
We have been talking about doing a joint testbed for a year. But they don’t have a process to approve it, so it sat there for a while until I had the crazy idea: just run one of our testbeds on their infrastructure and call it joint. When they call it joint, great, alles in Ordnung. In the meantime, it is running now.
Our first test bed, Track and Trace, runs in Germany. Our next testbed was in Ireland, and the next one was in California
How many testbeds do you have now?
Soley: We have a little less than 30. We have one focused on agriculture in India. One in Japan is focused on healthcare. We are in the middle of doing an automotive one in Germany with the support of a Korean company. We are about halfway through setting up one in mining in Northern Chile. About 40 percent of our testbeds today are in manufacturing and production. We have a few running live at Hannover Messe including the Time Sensitive Networking Testbed, which demonstrates interoperability between real-time networks: real-time Ethernet, UPS, OPC UA and so forth.
Which of the testbeds stand out in your mind?
Soley: The one we are doing in mining blew my mind. The Chilean state-owned copper mining company CODELCO is the biggest copper miner in the world. One-third of the copper in the world comes from Chile. They lost a miner two months ago. He fell off his truck. His helmet went flying off and he hit his head. They didn’t know for two hours. Had they known earlier, they might have saved his life. When they found him, he was dead, but he might have been alive for a while.
Part of the problem is the safety network in mines is bells, whistles and megaphones. It’s not because they aren’t high tech. They are one of the high-tech companies in the world. They have autonomous vehicles that are moving the ore around. They have all kinds of automated systems. But it is difficult to use Wi-Fi in copper mines because of multipath interference. The Wi-Fi signals bounce around, and you get interference from your own signal. It is too noisy. You can’t build a normal network in the mine.
I was recently speaking with the head of innovation at CODELCO, and he said: “I don’t want to lose any more miners. I want to work on safety first. Solve that problem for me, and you’ll make me a happy man.”
We are putting together a testbed for mine safety.
I recently spoke with a helmet maker. The company has a helmet with a computer inside that knows if it is on or off and a jacket maker that has a built-in point-to-point line-of-site router integrated into it. So you could send a signal from miner to miner and get around the multipath interference problem. There are many technologies to do that. Light, laser, and some RF / UHF technologies.
I was talking to the chief engineer at CODELCO, and he said: “If I use a point-to-point system like this, I can only see as far as my miners.” To which I replied, ‘Isn’t that the point?’”
What is also interesting is that CODELCO wants to link the system directly the health records of the miners. They want to know if a miner who has had a concussion in the past six months is not wearing his helmet. That is useful data.
And they are looking at using the smart helmet to look at pressure change. Increasing pressure means the mine is collapsing.
Which of your testbeds are furthest along?
Soley: Track and Trace is the furthest along. It is three years old and is in phase two.
Microgrids is two years along.
Our smart city project is now two-and-a-half years old.
Time Sensitive Networking is quite mature but it is only about a year and a half old.
The reason I always mention the Bosch Track and Trace Testbed is because the results are already going into real factories — in all 250 Bosch manufacturing centers worldwide.
Does a single industry stand out in your mind in terms of IoT adoption?
Soley: To me, airplanes are magical. GE’s IoT platform Predix was designed for jet engines, which, by themselves, are roughly as complex as the rest of the jet. I like the concept of renting jet engines rather than buying them: propulsion as a service.
GE’s idea was: we could generalize Predix for a whole bunch of issues. They have already changed their jet engine business.
The same thing is happening with elevators. There was a U.S. elevator company that historically made more money on elevator service from big elevator users than manufacturing elevators. Another company came along and said: ‘We will provide the same service for half the price. We can do that by installing a box into the elevator that communicates with our headquarters and warns us when there is a problem. That took away 70 to 80 percent of this other company’s business in three or four years.
What do you see as the main things holding back industrial IoT adoption?
Soley: Many people say the main trouble is security and the lack of standards. But people are going to buy it no matter how bad the standards are and how bad the security is. You can see proof of that everywhere you look. Lack of talent is a real challenge. If you want to find somebody who has built an IoT system today, there are not many people to hire.
I’ve heard the same thing about data scientists.
Soley: Well, my daughter is a theoretical quantum chemist. She read a book on data science and she said: ‘Dad, this is what we call statistics.’ There are only so many data scientists but there are plenty of statisticians.
Where do you think we are now in terms of IIoT adoption?
Soley: There is always a consolidation phase with new technology. It hasn’t happened yet with IoT.
I just read in somebody’s report that there are 1000 different IoT platforms. Everything is an IoT platform. There has to be consolidation because, right now, many of those platforms are not interoperable. What is going to drive it to happen? Testbeds.
Read more about:
IoT World TodayAbout the Authors
You May Also Like